-
Across Europe, companies in the industrial sector are striving to reduce costs associated with energy consumption. As these costs continue to rise, they have an impact on financial results and return on investment (ROI). The planet is also affected by the use of industrial energy, which accounts for 26% of global greenhouse gas (GHG) emissions, according to the IEA.
In the UK, although the manufacturing industry has made the greatest reduction in emissions between 1990 and 2019 (-46%), it still ranks fourth in terms of GHG emissions, accounting for 18% of total emissions. Thus, the UK still has significant efforts to make, particularly in this sector, to achieve carbon neutrality by 2050. So, how can we help industries reduce their energy footprint?
In this article, discover five measures that you can implement today to reduce the burden of energy costs in the manufacturing industry, regardless of your sector of activity.
How to Reduce Your Production Energy Costs?
1. Set SMART Goals for Your Teams
Today, speed and efficiency are fundamental aspects of industrial manufacturing and modern production processes. However, it can be challenging to achieve both goals due to unpredictable system failures, uncontrolled overhead costs, and energy waste.
To achieve production goals quickly and efficiently, industrialists must align their operational performance with a comprehensive energy strategy and involve the right people in its implementation. They can establish a team responsible for defining and achieving SMART energy management objectives.
For example, TACSA, a Spanish industrial metallurgy plant, saved €110,000 by designating a dedicated energy team to set, implement, and continuously review its SMART energy goals.
Once these objectives are clearly defined, we recommend involving employees in your approach. An energy efficiency plan should not be solely led by management teams or energy managers. Such a project should be collaborative and supported by all stakeholders in the company. In the coming article, we will discuss how to develop an energy culture by improving knowledge and raising awareness of proper energy use, we have got a strategy that works for many.
2. Monitor and Analyze Your Energy Consumption
Every piece of machinery in your factory holds valuable data that can reveal low-cost or cost-free measures to eliminate energy waste, which contributes to unnecessarily high bills.
For example, installing real-time energy monitoring and analysis systems will enable your team to have full control over your energy consumption. You can also take advantage of alerts triggered by these monitoring tools, which will help you prevent equipment breakdowns and failures in the factory.
This monitoring also allows for consumption savings during non-production hours, as was the case with the TACSA metallurgy plant. It is essential for you to know the hours, days, and processes that generate the highest energy consumption in your factory. By doing so, you can avoid peak-time tariffs and adjust your operating hours accordingly.
3. Switch to LED Lighting
Previously, it was advised to replace fluorescent lights with low-energy bulbs. However, it is now recommended to switch to LED lighting. With a lifespan of 100 times longer than incandescent bulbs, industrialists can achieve energy savings of up to 80%.
With this argument, it is impossible for your CFO or energy manager to reject your energy efficiency project proposal, isn't it?
Moreover, LED bulbs offer numerous advantages. Their superior lighting quality enhances safety and productivity within your factory's working environment.
4. Check Your Contracted Power
When we talk about power factor, we refer to the ratio between actual (active) power and the apparent power that supplies an electrical load (e.g., a packaging machine in your production factory).
In other words, this factor measures the efficiency of an electrical load in converting electrical energy into useful power, such as light, heat, or mechanical movement. However, it happens that not all the electrical energy consumed by these loads is completely transformed into useful energy. Therefore, it is important for industrialists to understand how a miscalculated contracted power (power factor) can increase their energy bills.
When a motor operates inefficiently, the apparent power (measured in kVA) increases, resulting in higher energy consumption typically billed per kilowatt (kW). In such cases, some suppliers penalize customers with too low contracted power, unnecessarily driving up their energy bills.
Hence, it is crucial to check the contracted power with your supplier, especially if you have recently installed more efficient equipment or upgraded some of your machinery. Keep in mind that simply adjusting the contracted power can lead to savings of up to 50% without any cost.
As the energy supply market becomes increasingly deregulated, UK and European industrialists can negotiate more with different suppliers and benefit from reduced production process costs. However, without accurate information about the consumption profile of your facilities and processes - which you can define through energy monitoring and analysis - achieving this can be challenging.
5. Seek Alternatives to Reduce Energy Waste
Have you ever heard of the term "waste heat" or "wasted heat"? It refers to the heat produced by your machines during the creation of products and by-products. This residual heat can be converted into energy that can then be reused in other production processes in your factory. We will soon share an article that explains how waste heat can be harnessed and the benefits of its utilization in your factory.
Measure the Impact with Technology
Are you ready to implement a plan to reduce your costs and improve your carbon footprint? If so, you are on the right track!
For your plan to be successful, we highly recommend tracking your actions using technology. Implementing a tool such as an Energy Management System (EMS) will help you identify areas (e.g., specific machines or zones in your factory) that require energy efficiency measures. Moreover, you will be able to monitor and verify the proper functioning of these measures in real time.
By implementing an EMS like the Cloud SkySpark.Connect Platform, you can easily and automatically detect potential leaks and anomalies, analyze, see how these issues are costing you, and how much you will be able to save once you resolve those issues and optimize your energy consumption. If you want to know how to improve your energy performance with such a tool and move towards smarter manufacturing management, please do not hesitate to contact us.
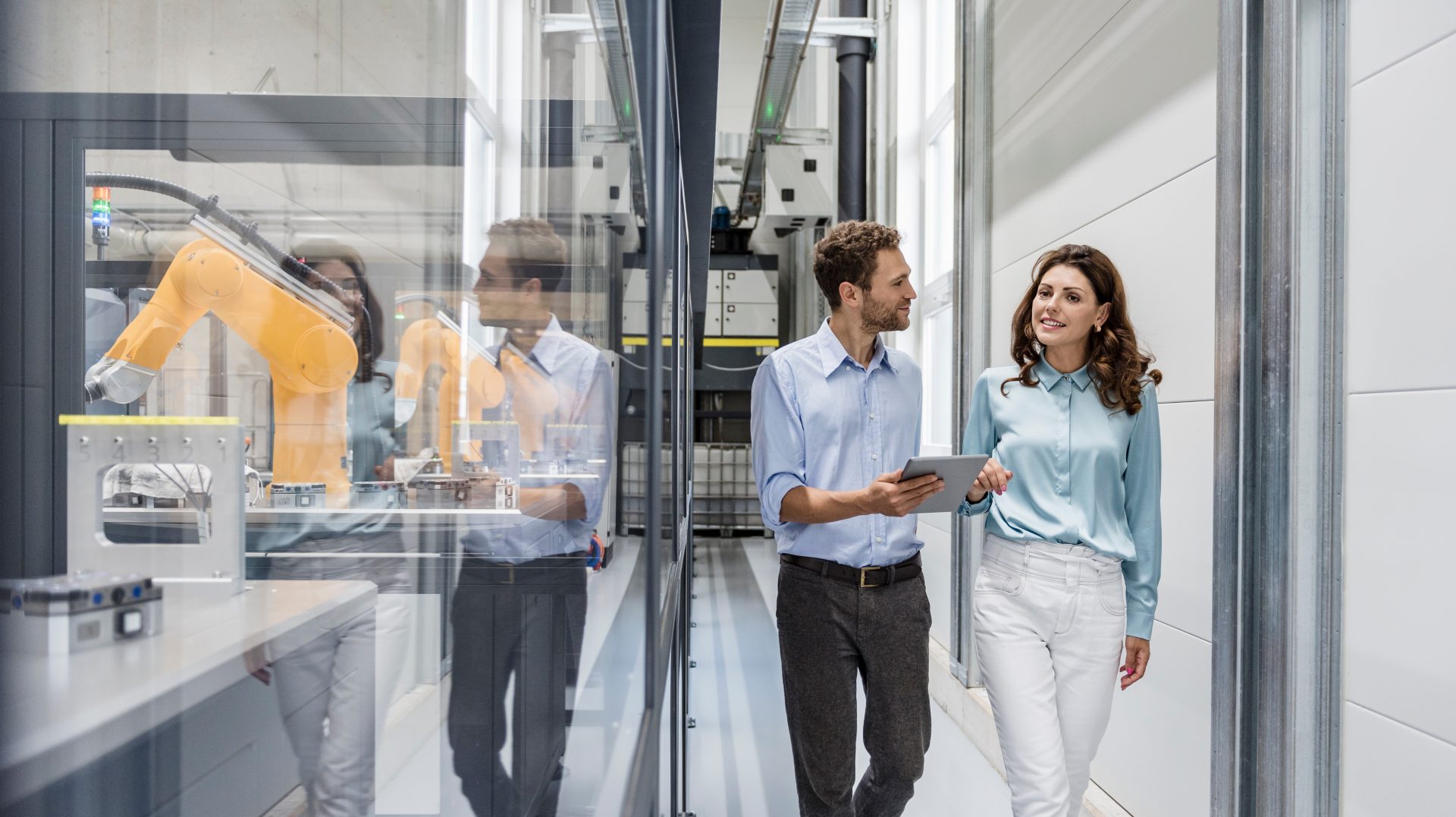